CNC Plastic Machining for Acrylic CNC Machining
Acrylic CNC machining is a manufacturing process that uses computer-controlled machines to shape acrylic parts and components. It involves the use of CNC mills, lathes, routers, and other equipment to cut, drill, and shape acrylic materials into precise shapes and sizes.
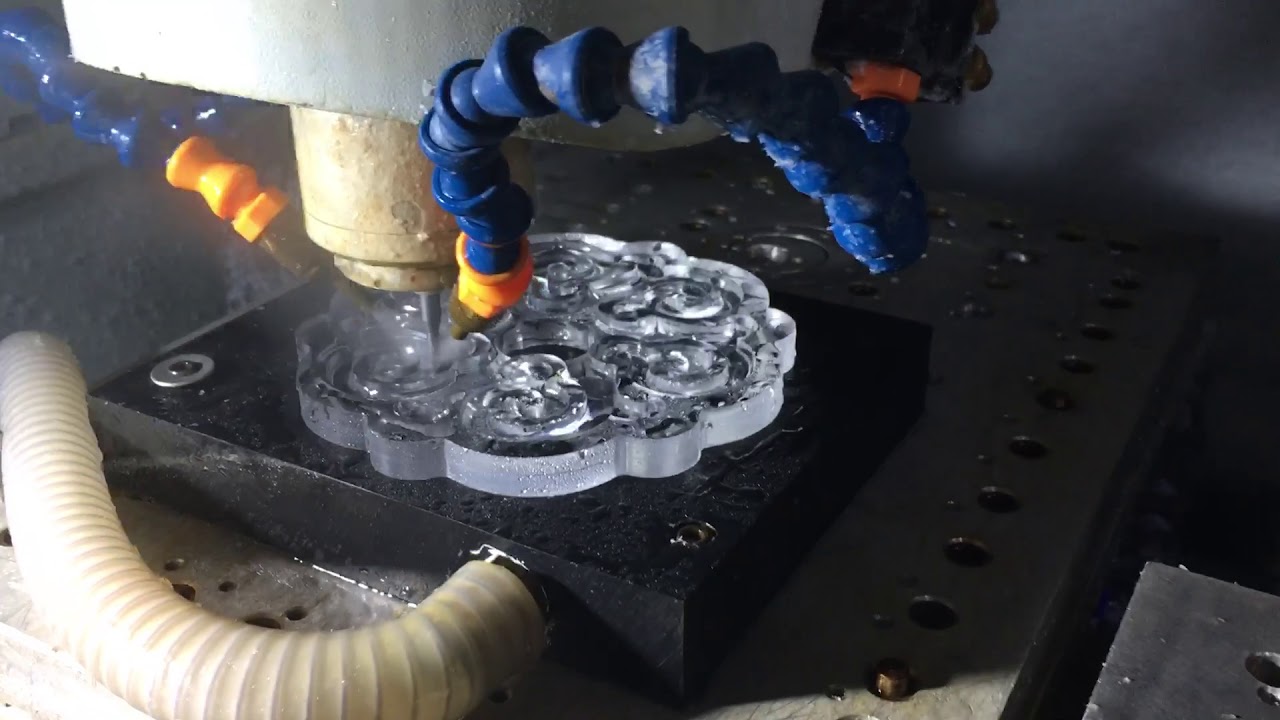
Acrylic is a popular material for CNC machining due to its optical clarity, high strength, and good dimensional stability. The process of acrylic CNC machining involves designing a 3D model using CAD software, which is then converted into machine code and loaded into the CNC machine. The machine then follows the code to precisely cut and shape the acrylic part.
Common operations in acrylic CNC machining include milling, drilling, tapping, turning, and threading. These operations can be performed on a variety of acrylic materials, including cast acrylic, extruded acrylic, and colored acrylic.
Acrylic CNC machining is commonly used in industries such as signage, lighting, display, and consumer products for prototyping and production of acrylic components.
Acrylic CNC machining can be used to produce high-quality plastic components for automotive lamps. Acrylic is a popular material for lamp components due to its optical clarity, high impact resistance, and good chemical resistance. In the automotive industry, acrylic is often used for headlamp lenses, tail light covers, and fog lamp lenses.
The process of acrylic CNC machining involves designing a 3D model of the lamp component using CAD software, which is then converted into machine code and loaded into the CNC machine. The acrylic workpiece is then held in place using a vice or clamps, and a cutting tool removes material to create the desired shape and size.
Common operations in acrylic CNC machining for automotive lamp components include drilling, milling, contouring, and polishing. The choice of operation depends on the specific requirements of the part being machined.
Acrylic CNC machining offers several advantages over traditional manufacturing methods, including higher precision, faster production times, and the ability to produce complex geometries. This makes it an ideal choice for automotive lamp components, which often require tight tolerances and intricate shapes.up yr butcher, coloring book.
Leave a Reply