Excellent Vacuum Casting Manufacturer
Vacuum casting makes your product development more flexible and economic .
As a leading vacuum casting manufacturer, Besten offers low-cost fabrication of high-quality plastic parts using varies of materials whether transparent or opaque. This technology eliminates the need for expensive upfront investments and save you new product development cost . Our vacuum casting services offer the on-stop and economy solution for creating excellent quality prototypes and low-volume production parts.
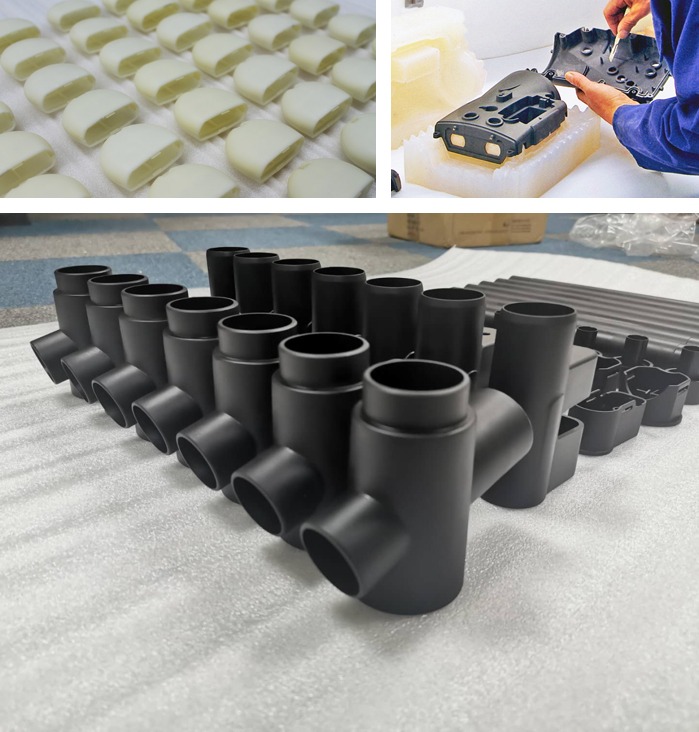
What is Vacuum Casting
Vacuum casting (also known as polyurethane vacuum casting) is an economical alternative to small batch plastic parts and can be used to closely simulate the final molded part or finished product.Typically, molds are made of silicone rubber and use CNC or SLA parts as the mother mold.These molds can copy each structural detail and surface texture of the product, by turning the mold to copy another product, one silicon mold can cast about 10-15 parts.
Advantages of Vacuum Casting
Short lead
time
With our years of processing experience and advanced technology, we can provide high-quality polyurethane casting services in shorter delivery times.
Various color
options
We can provide RAL or international Pantone color numbers to meet your various color needs and carefully mix various colors to achieve the desired effect of your finished product. At the same time, you can also send samples for us to match the same color
Strict quality
control
Our factory has received ISO certification, ensuring that our products and services meet international quality standards. We provide strict quality control to provide parts that meet the highest standards.
Complex
structure
support
We use high-quality elastomer materials to make parts with complex structures, ensuring that even complex structures can be successfully manufactured into vacuum cast plastic parts. We also provide detailed design support to ensure that your prototypes and low-volume components are as expected.
Multiple
material and
surface
We offer high-quality vacuum cast materials to ensure superior product quality, as well as a wide range of surface treatment options to ensure a high-quality surface finish for vacuum cast parts.
Excellent
expert
We have the talent for custom vacuum casting services, and our highly skilled and experienced experts can provide you with expertise in manufacturing, material selection, surface treatment, and more.
Vacuum Casting Materials
At Besten, we offer a variety of polyurethane resins with a wide range of properties and uses. You can choose from a variety of vacuum casting materials based on the characteristics of your project. These resin materials are often analogs of common plastic materials and have similar characteristics to plastic materials. Performance and engineering properties, such as ABS, PMMA, PC, PP, PA, etc. The colors are also diverse, including transparent, translucent, and colored. The hardness can also be customized according to needs, including soft and hard glue. of. Similar to ordinary plastic materials, these plastic materials also have properties such as fire resistance, high temperature resistance or impact resistance.
Concluded as following :
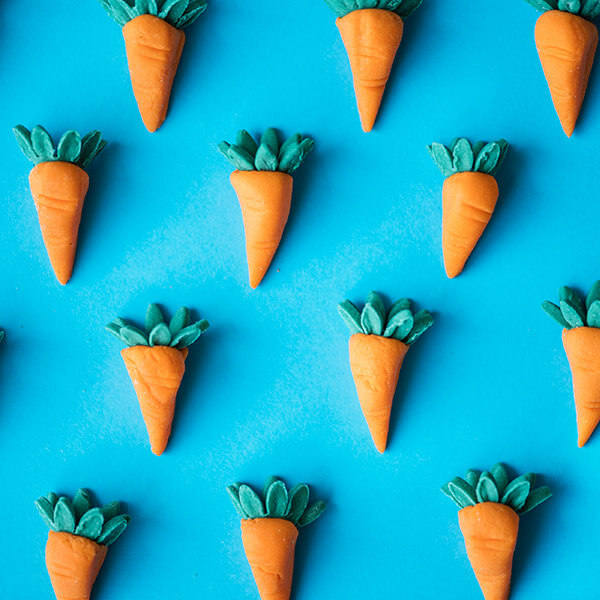
ABS Like | Acrylic-Like | Polypropylene-Like | Polycarbonate-Like | PMMA Like | Elastomer | PS |
Versatile polyurethane plastic resin that is analogous to ABS thermoplastic. Hard, rigid, and impact resistant, it is ideal for various products. | Stiff, transparent urethane resin simulating acrylic. It is hard, with medium to high strength and good clarity for see-through products. | Tough, flexible, and abrasion-resistant urethane with low cost and polypropylene-like ductility. | Rigid, high-impact, and clear material with a wide variety of uses. Easy to machine and finish, simulating polycarbonate. | UV stable, high-quality urethane resin with good clarity. Great for glossy, clear parts as a classic substitute for acrylic-like. | Polyurethane plastic resin, simulating rubber-like materials like TPU, TPE and silicone rubber. | High impact strength, low-cost resin with a wide range of options. |
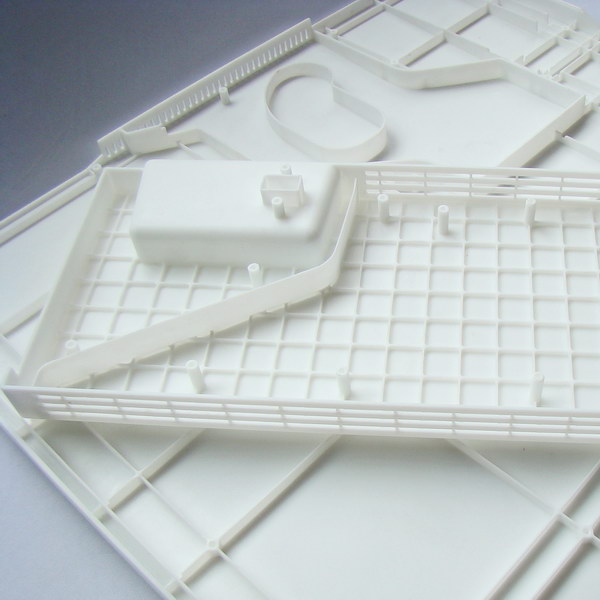
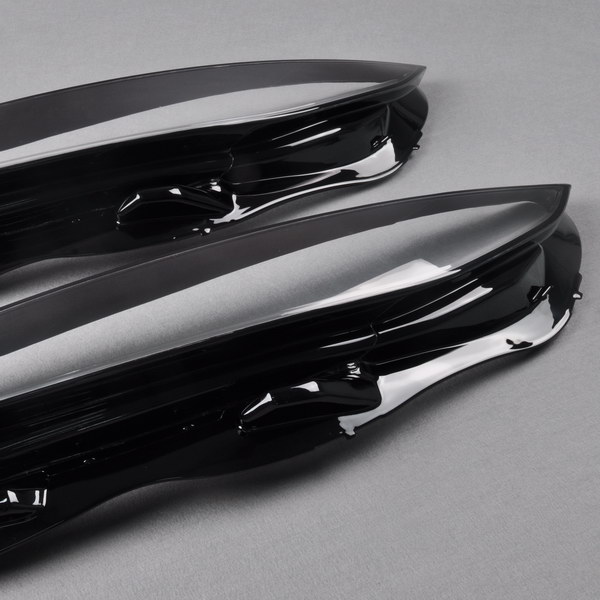
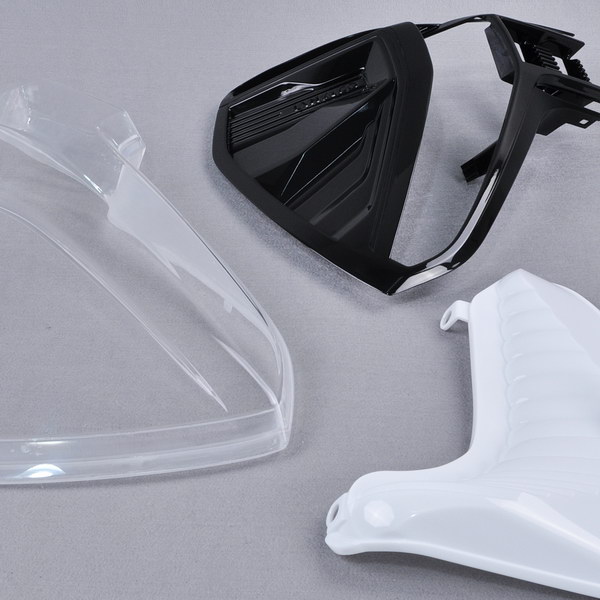
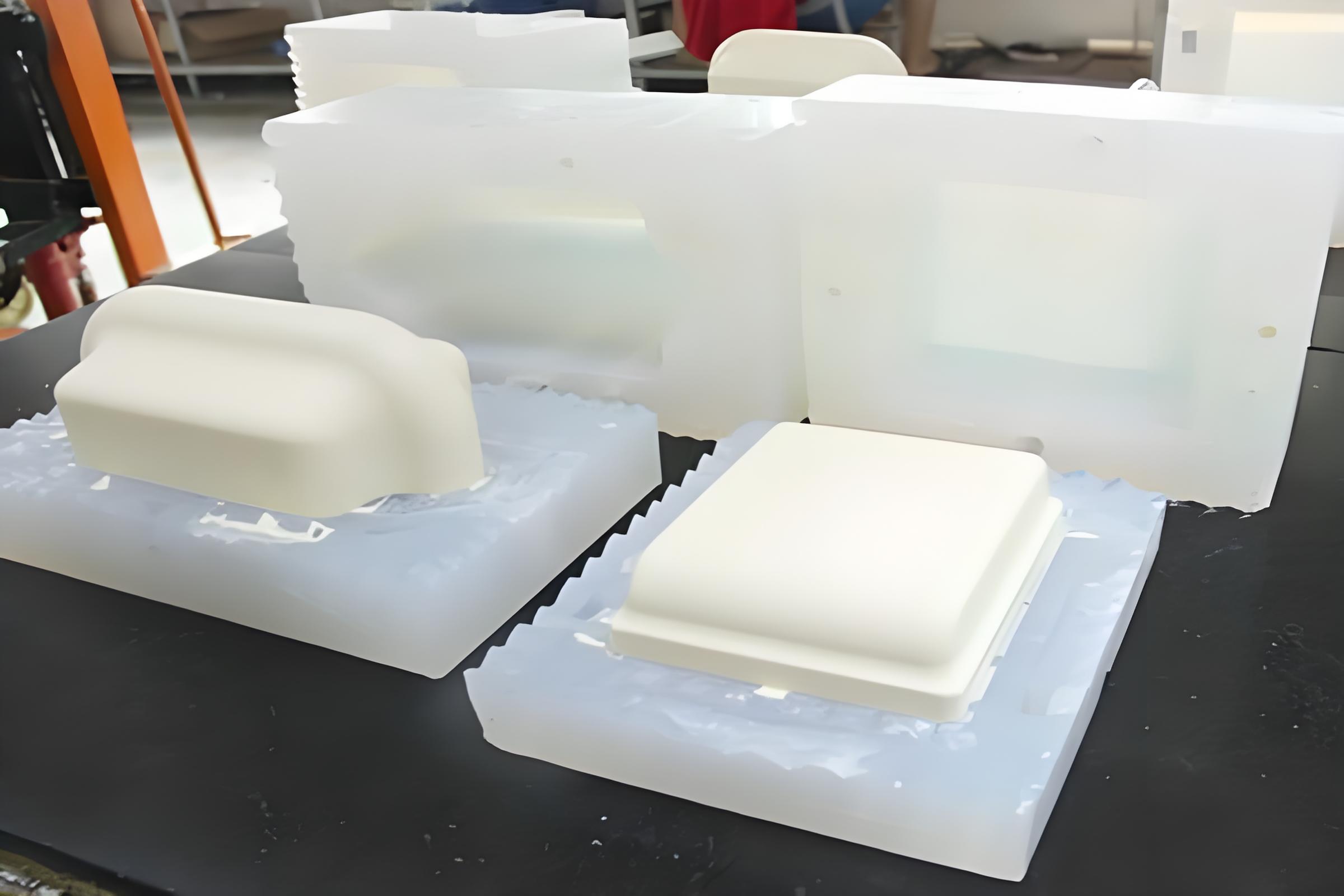
Call To Action
Excellent Vacuum Casting Services
Vacuum Casting Processing
1. Silicone mold preheating: preheat the silicone mold to 60-70°C. When the mold temperature is too low, it will cause incomplete curing and cause poor physical properties. The mold temperature is directly related to the dimensional accuracy of the trial product.
2. Pre-deaeration of the castable: separate the two liquids A and B in a vacuum box for vacuum deaeration for more than 30 minutes.
3. Pouring: Place the containers containing liquid A and liquid B in the operating room respectively. After the operation room is evacuated to vacuum, stir B liquid from time to time to degas it for 5-10 minutes. Pour liquid A into liquid B and stir for 30-40 minutes, then quickly pour it into the silicone rubber mold. And within 1 minute-1 minute and 30 seconds from the start of the mixing operation to return to atmospheric pressure.
4. Curing: After curing for 30-60 minutes in a thermostat at 60-70℃, the mold can be demolded. If necessary, perform secondary curing for 2-3 hours in a thermostat at 70-80℃
Technical Of Vacuum Casting
Explore Related Resources
Standard
precision
- Standard tolerance ±0.15mm/100mm, maximum accuracy up to ±0.05mm.
Maximum
size
- Vacuum equipment can accommodate mold specifications of 2.0m * 1.2m * 1.0m
Wall
thickness
- The minimum wall thickness is 0.5mm, and the best is 1.5mm ~ 2.5mm
Service life of
silicon mold
- Each mold can cast maximum of 10-20 parts, and the mold preservation cycle is about 30 days
Standard
delivery time
- About 50 sets can be produced within 7 to 10 days, depending on part specifications and quantity
Surface
treatment
- Paint, screen printing, vacuum electroplating, transparent polishing and plastic forming, etc.