CNC machining parts are parts processed by CNC equipment. CNC machining usually refers to a precision machining method controlled digitally by a computer. It has now become a common machining method.
CNC processing equipment is called CNC machine tools, also called numerical control machine tools. It also has different names in different regions. For example,In China, the Yangtze River Delta area is usually called a machining center, and the Pearl River Delta area is usually called a computer gong.
Typical CNC machine tool:
1. CNC Lathe – A lathe works by rotating the material in the lathe’s chuck. The tool is then moved into the workpiece along 2 axes to cut the cylindrical part.
2. CNC Milling Machine – CNC milling machines are typically used to make flat parts, but more complex machines with more degrees of freedom can create complex shapes; the material remains stationary and the spindle rotates with the tool, which spins along 3 axes (some are 4 axis or 5-axis) moves or rotates to cut into the material; in some cases, the spindle is stationary and the material enters it.
3.CNC Drill Machines – These machines are similar to CNC milling machines, but they are specifically designed to cut along only one axis, i.e. the drill only moves down into the material along the Z axis and never cuts along the X and Y axes.
4.CNC Grinder – These machines move a grinding wheel into the material to produce a high-quality surface finish. They are designed to remove small amounts of material from hardened metal; therefore, they are used as finishing operations.
Compared with traditional machine tool processing methods, the advantages and disadvantages of CNC processing are as follows:
A dvantage | Disadvantage |
faster than manual No one can match the speed, precision and accuracy of CNC machine tools. In high production environments, using manual machines will only lead to financial losses. | expensive CNC machine tools are extremely advanced equipment. Its manufacturing tolerances and stiffness are very high. This is to enable it to manufacture millions of parts and still produce high-quality results. This quality translates directly into cost, and the more advanced the machine, the higher the cost. |
reduce manufacturing cost If the loading and unloading of materials and parts is further automated, CNC machines can run essentially non-stop, meaning the machines can run all night long without supervision. Additionally, one operator can run multiple machines, offsetting higher labor costs. | Highly skilled operator Although fewer operators are required, CNC machine tools require highly skilled operators, which will result in higher labor costs. |
higher efficiency CNC machines can move from one operation to the next in a fraction of a second. Tool changes are very fast because some machines have many tools preloaded in the turret, or a tool magazine can load new tools into the spindle when needed. | Higher maintenance costs Due to the complexity of CNC machine tools, maintenance costs are much higher compared to manual machine tools. |
CNC machining is widely used in various industries due to its high-precision characteristics. However, CNC machining services can also be more expensive compared to other manufacturing methods such as injection molding, die casting, stamping, etc. The main factors that affect the cost of CNC machined parts are the following:
1. Processing equipment
Equipment costs include initial purchase costs, operating costs, maintenance costs, etc. There may also be some other costs, such as tool costs, CNC system usage costs, etc. These costs will affect the cost of each machined part. Therefore, purchase, operation and maintenance The more expensive a machine is, the more expensive the parts made using that machine will be.
Milling machines generally cost more than lathes because they have more complex moving parts; are more difficult to set up, operate, and maintain; and are capable of more complex machining. Therefore, if necessary, the parts should be designed to adapt to lathe processing.
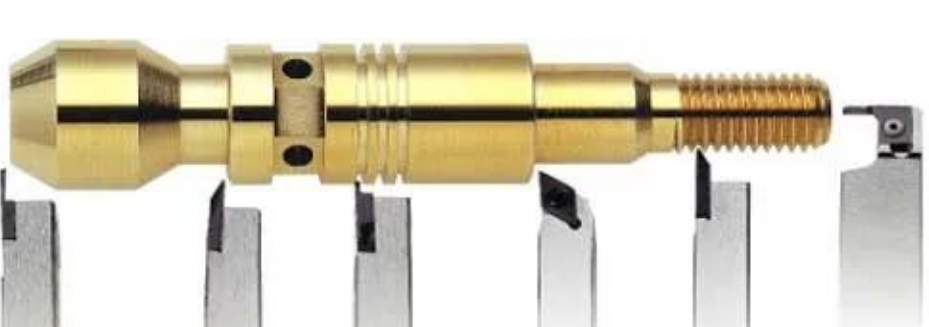
There are different types of milling machines with varying levels of sophistication and capabilities. The more axes a milling machine has, the higher the price. Most modern CNC machine tools have three or five axes. While 5-axis machines can create very complex geometries more accurately and faster (so they require less machining time), they are generally more expensive than 3-axis machines.
2. Design cost
Design cost is the cost incurred in preparation before actual processing, which mainly includes the costs involved in the CAD (structural and engineering drawing design), CAE (optimization analysis), and CAM (manufacturing programming) processes. The costs incurred by CAD and CAE may not necessarily be allocated to the cost of parts. This depends on the cooperation method of Party A and Party B. At the same time, the design cost is fixed. The larger the quantity, the lower the design cost allocated to each part.
3. Material cost
The material cost involved in manufacturing parts is one of the most important parts cost components. The material cost consists of the cost of raw materials, the amount of materials used, and the processing time of the materials.
Raw material cost: The market prices of different raw materials are different, and the prices in different market areas are also different. When selecting raw materials for parts, you should choose appropriate materials based on the use and function of the parts, rather than choosing materials that exceed performance requirements. Expensive materials, such as 316 stainless steel, which is both stainless steel, are much more expensive than 304 stainless steel.
Amount of material: When designing the part structure and manufacturing process, the amount of material should be considered as small as possible. If necessary, two relatively simple parts can be disassembled to form a complex part through subsequent assembly (more is needed) material usage and processing time).
Material processing time: The cost of a part is directly proportional to the time required to process it. The processing time of the material is related to the machinability of the material. Materials with low machinability require more time to process and will also consume more resources, such as cutting fluid, electricity and cutting tools. (For example, softer materials such as aluminum alloys are easier to cut, which means shorter machining times; while harder materials such as stainless steel require more expensive machining tools and are more likely to damage and wear tools, making the parts more expensive to machine. high.)
4. Production volume
As the number of parts increases, the unit cost of a set of identical parts decreases significantly. This proportional cost reduction is primarily the result of eliminating duplicative design costs and machine setup commissioning. CAD design, CAM preparation and machine setup are done in one go for all parts to be manufactured. (In other words, when producing a part, the design cost and machine setup cost are included in this part. If 1,000 pieces are produced, the design cost and machine setup cost will be evenly spread over the 1,000 pieces.
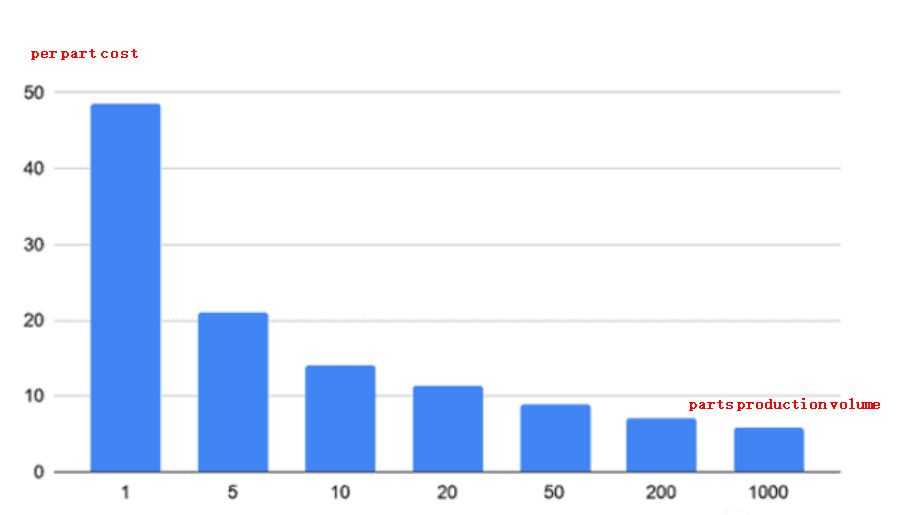
5. Special requirements
Before processing CNC machined parts, tolerance requirements and surface roughness requirements need to be clearly defined. Stricter tolerance requirements will make it more difficult to process and increase the scrap rate, which will also lead to higher costs; higher surface roughness requirements may As a result, CNC milling machine processing cannot be performed, and grinders or other methods must be used, which increases the process and naturally increases costs.
After the CNC machined parts are processed, some post-processing may be required, such as heat treatment, surface treatment, etc., to improve the function, performance and aesthetics of the parts. These post-processing requirements will increase the cost of the parts to a certain extent.
For surface preparation, another serious cost driver is applying different surface preparation requirements to different areas of the part. For example, partial plating, partial anodizing, two-color prototype oxidation, oxidation in one area and electroplating in another area. Therefore, in order to reduce costs, the surface treatment requirements of the entire part should be kept consistent if necessary.
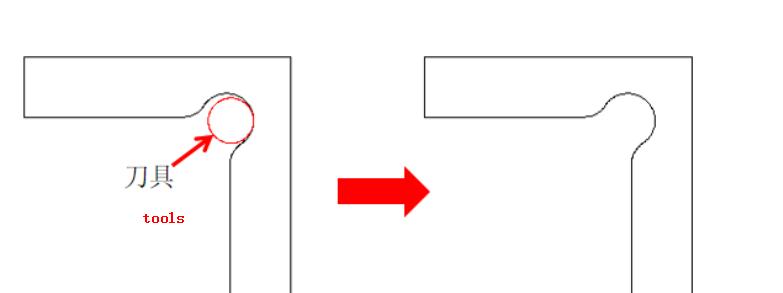
6. Structural design
The more complex the part structure, the higher the manufacturing cost. Highly complex parts may require more advanced machinery. They also require more processing time, multiple assembly and disassembly and equipment setups, more resources and closer inspection. All of this affects the cost of the part.
In CNC machining, certain part features and designs inevitably increase costs.
1) Avoid thin-walled designs
Machined parts with walls that are too thin will take more time to machine because they are very fragile. And because they often vibrate or deform, it can be difficult to maintain accurate tolerances or, in worse cases, breakage. Slow machining, specialized machining techniques and high scrap rates make these thin-walled parts more expensive.
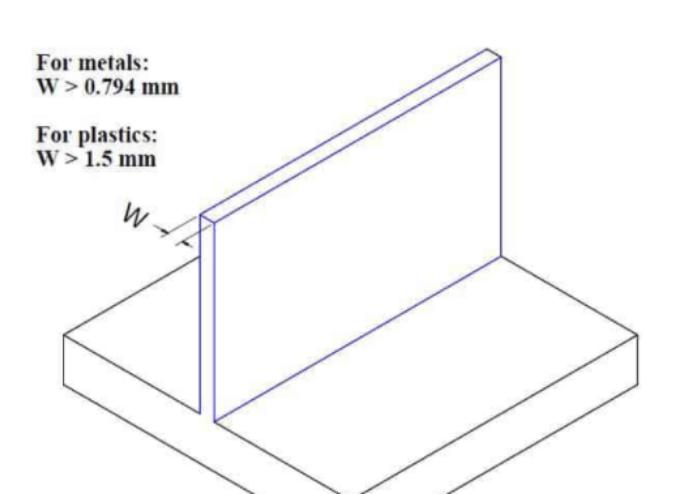
The processing of thick-walled parts is more stable and the processing cost is lower. In order to keep the processing price low, please avoid thin-walled designs. The wall thickness of metal parts should be greater than 0.8mm, and the wall thickness of plastic parts should be greater than 1.5mm.
2) Avoid designing features that cannot be CNC machined
Not all features can be CNC machined. A typical example is a 90° internal angle. Since all current CNC milling tools have a cylindrical shape, cutting the edge of the cavity will produce a rounded corner instead of a right angle or other sharp angle.

If a right angle must be left, the usual way to achieve this is through EDM (electrical discharge machining), a more expensive manufacturing process than CNC machining. If the rounded corners cannot be left only for assembly reasons, it is recommended to use inscribed rounded corners, as shown in the figure below.
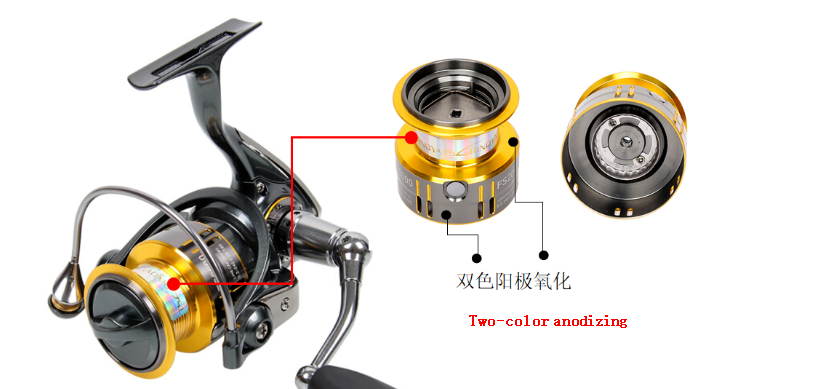
3) It is recommended to design a larger internal corner radius
While using a smaller diameter tool can reduce the corner radius, this means multiple passes at lower speeds because the smaller tool cannot remove material in a single pass as quickly as a larger tool. , so small fillets will also increase processing time and cost. It is recommended that the fillet radius R is at least 1/3 times the cavity depth D.
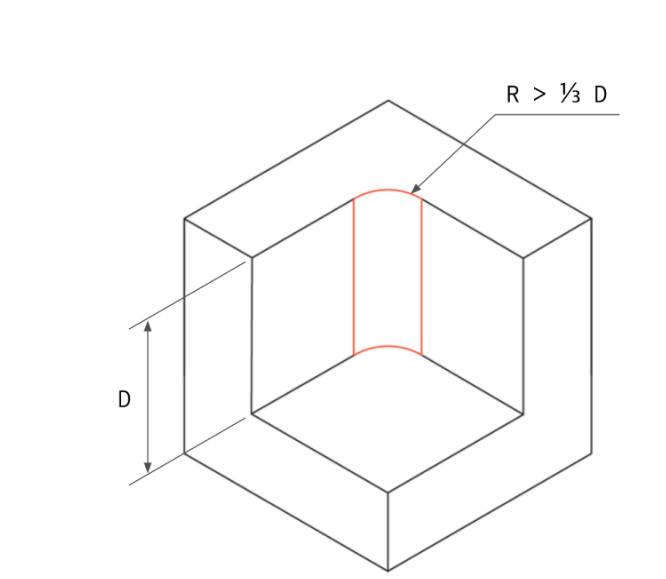
At the same time, to avoid tool wear, it is necessary to design internal edges that do not put too much pressure on the tool. To achieve this, a good rule of thumb is that the corner radius should be slightly larger than the radius of the tool used to machine the pocket (corner radius is 1.3 times the mill radius or greater). For example, if the milling cutter has a radius of 5 mm, it is recommended to add a radius of 6.5 mm to the internal corners. This extra radius will reduce stress on the tool and increase cutting speeds.
4) Limit the depth of the cavity
Machining deep cavities can greatly impact the cost of CNC parts because a large amount of material needs to be removed, which is very time-consuming. Too deep a cavity can lead to problems such as tool overhang, tool deflection, difficulty in chip evacuation, and tool breakage.
When the milling depth is greater than 2 times the diameter of the milling tool, the feed speed of the tool must be slowed down, which increases processing time and part cost. Every time the milling depth is doubled, the feed speed will be halved and the time will be more than doubled. Generally, the milling depth is not greater than 4 times the tool diameter. When designing, the maximum depth should be four times the width of the cavity, for example, a 15 mm wide cavity should not be more than 60 mm deep.
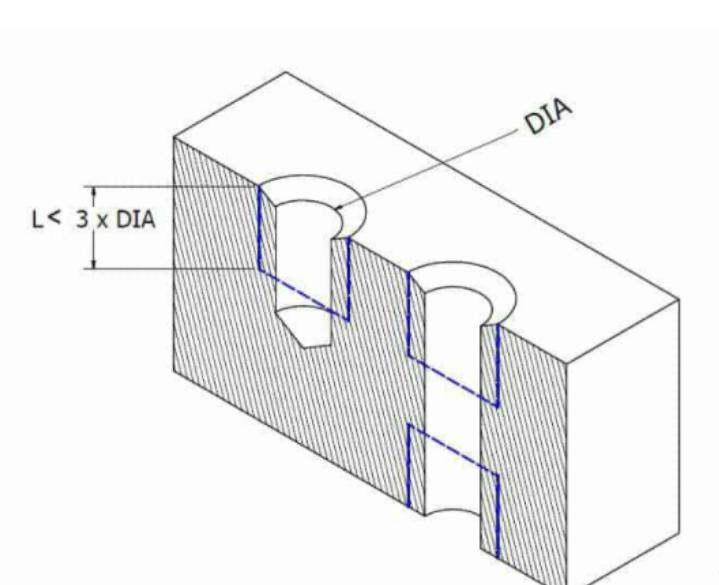
If deep cavities cannot be avoided, the solution to deep cavity machining is to gradually lower the end mill and mill layer by layer. However, this is also very time-consuming. Additionally, when machining deep cavities, the tool must be tilted to the correct depth of cut, and sufficient space is required for a smooth entry.
5) Reduce the use of surface structural features
When designing CNC machined parts, simple structures should be the principle, and the design of complex surface features should be reduced, because in order to obtain complex surfaces with suitable surface finish, small tools need to be used, and these small cuts take much longer than normal cuts. Added a lot of costs. Therefore, to help minimize costs and machining time, minimize or avoid the use of curved surfaces. For example, when chamfering outer edges, chamfer instead of round if necessary.
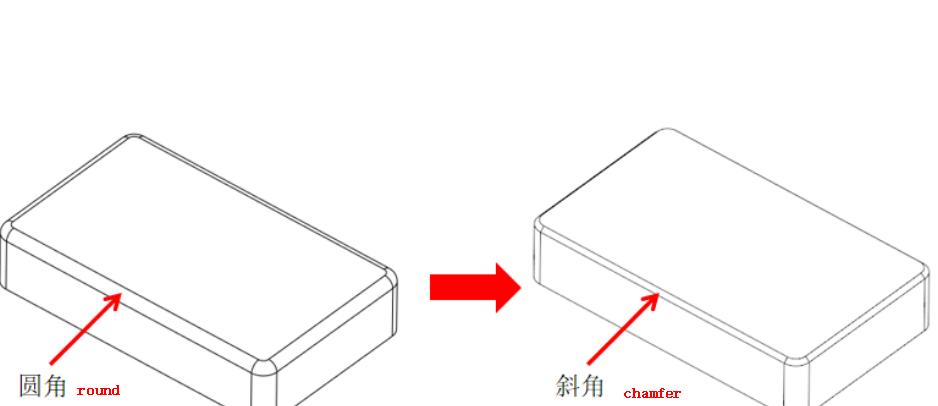
6) Limit thread length
As we all know, a strong thread connection occurs in the first few threads, so sometimes a long thread length is not required at all. Long threaded holes may require special tools and require more processing time, and the cost will also increase. The thread length is not recommended. More than 3 times the hole diameter. When the threaded hole is blind, it is recommended to leave an unthreaded length of at least half the hole diameter at the bottom of the hole.
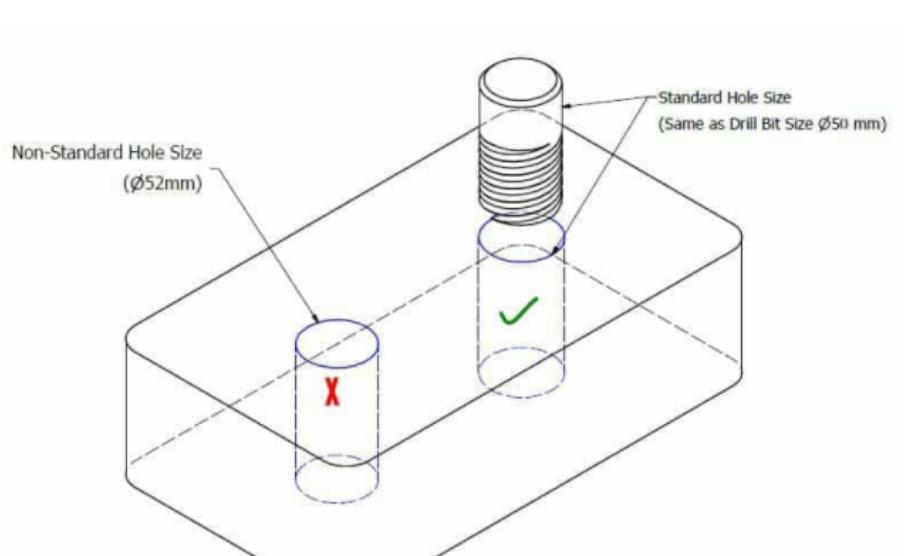
7) Design standard size holes
Holes can be CNC machined quickly and with high precision using standard drill bits. From an economic point of view, try to use standard hole diameters. For non-standard size holes, you must use an end mill to process the hole, which may increase costs.
In addition, generally speaking, the larger the hole, the deeper the drilling depth can be. It is recommended that the drilling depth should not exceed 10 times the diameter of the drill bit.
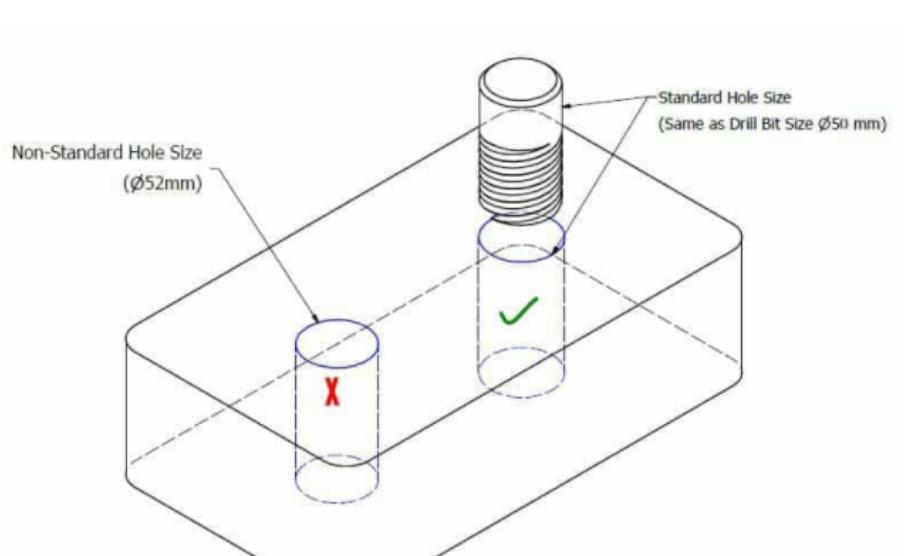
8) Keep the number of CNC machine setups to a minimum
Turning or repositioning parts increases manufacturing costs because it often needs to be done manually. Additionally, for complex geometries, custom fixtures may be required, further increasing costs. Particularly complex geometries may require multi-axis CNC systems, further increasing the price.
Therefore, in order to reduce the number of parts flipping and repositioning, you should try to design all features that need to be machined on one plane; if this cannot be avoided, consider splitting the part into features that can be CNC machined in one setup, and then use bolts Joined or welded together.
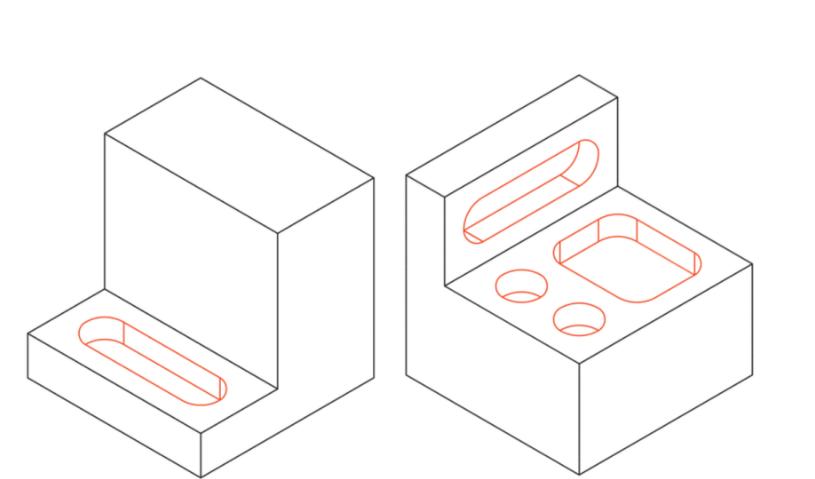
9) Avoid unnecessary text and lettering
Adding text features to the surface of CNC machined parts should be avoided, as designing text through CNC machining will only increase processing time and cost.
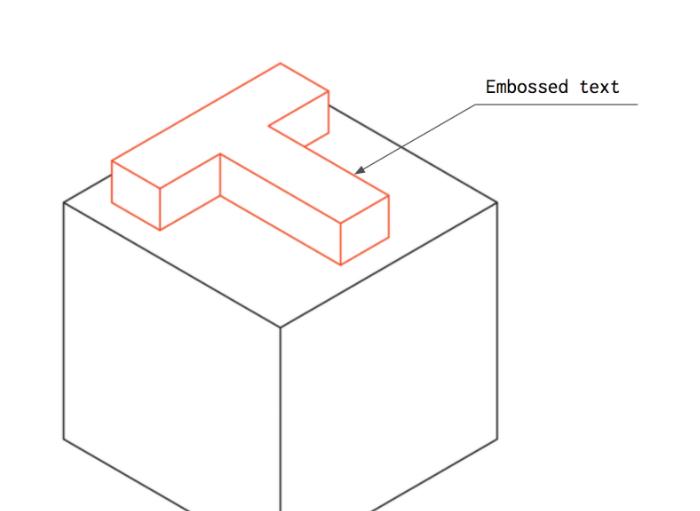
However, if text and fonts are design requirements, the following rules should be followed:
Adding text to the surface of CNC parts through silk screen printing or spraying is cost-effective.
On curved surfaces, laser engraving can be used because less material is removed in this case.
If your design software does not have a custom lettering font, it is recommended to use the 20-point San Serif font. This is because this font has no extra lines (serifs) at the end of each letter stroke. These extra trips increase processing costs. Additionally, size 20 is recommended because sizes smaller than this are considered smaller features and are more difficult and costly to machine.
Of course, there are many ways to reduce processing costs. Welcome to call or email Besten prototype for more details.
Leave a Reply