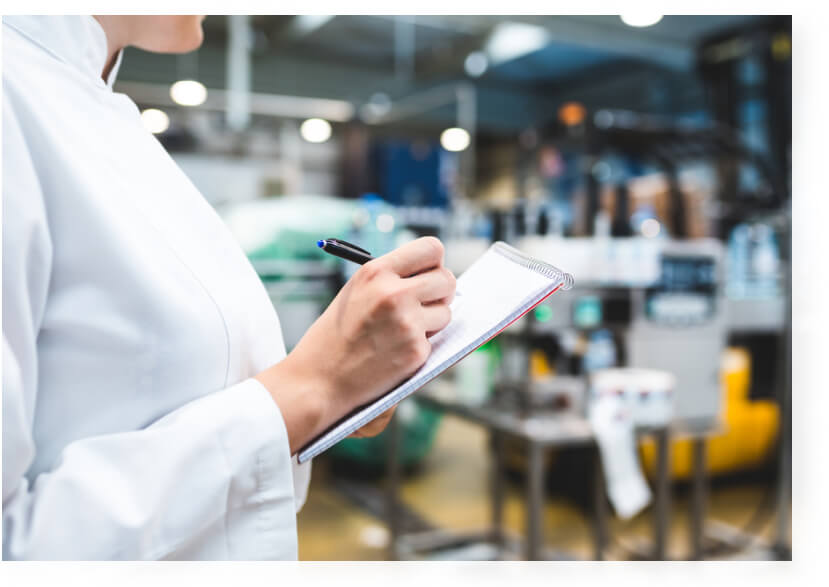
Engineering verification is a critical process within the product development lifecycle aimed at ensuring that a design meets specified requirements and performs as expected before moving into production. It involves rigorous testing, analysis, and validation of various aspects of a product or system to confirm its functionality, reliability, safety, and compliance with standards.It is a series of components created by combining engineering and design to represent the final product. Typically built using rapid prototyping, this robust and highly accurate pre-production prototype undergoes rigorous testing and evaluation to validate product design, engineering, and manufacturability.
Prototype engineering focused on optimizing mass production
Engineering prototyping and testing help uncover problems as product development moves into subsequent stages where design and engineering meet. Identify improvements and iterations before investing in expensive tools and putting them into production, making future production processes as smooth and reliable as possible.
Through a series of verification test processes, including basic functional testing, manufacturing process, performance parameter measurement and verification of certification standards, it can be verified that the design meets the expected product specifications and performance. The goal is to verify that the design has been correctly implemented into production.
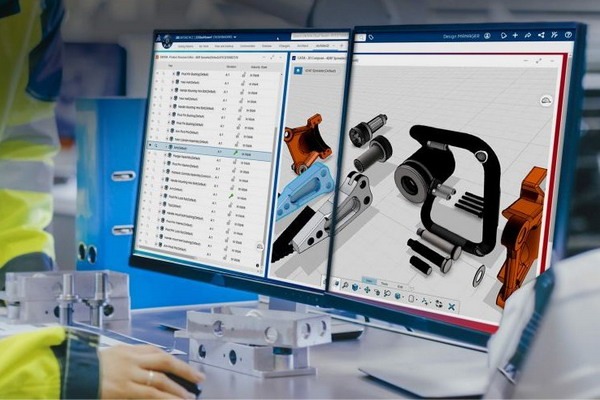
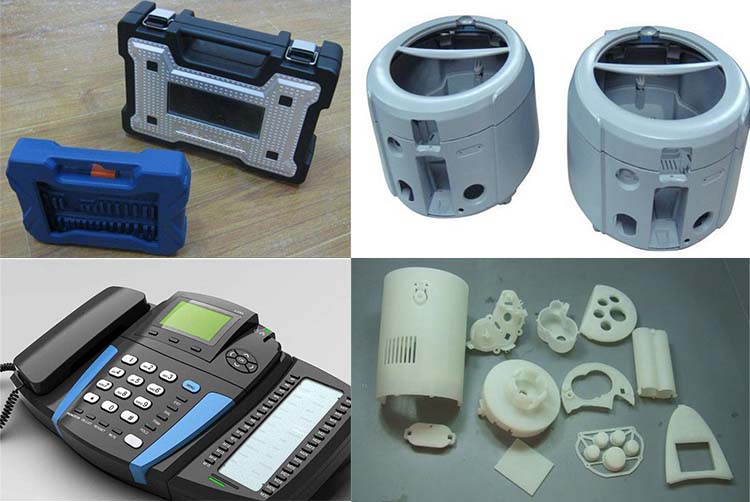
Picture Display
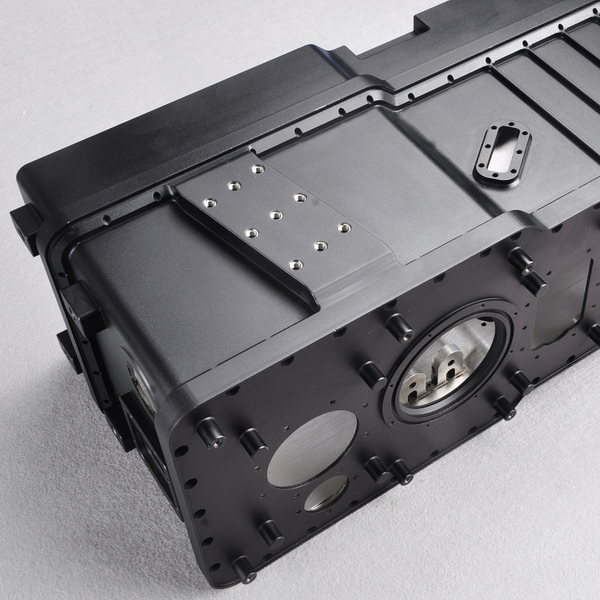
Aluminum Alloy Consumer Electronics
Zamak alloy CNC machining
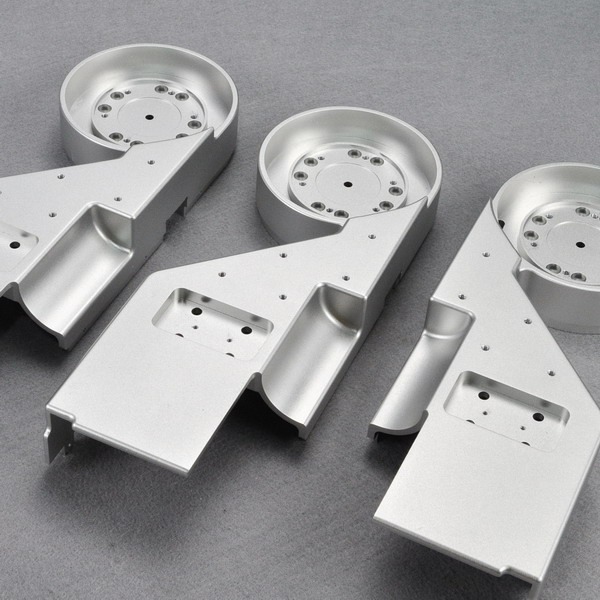
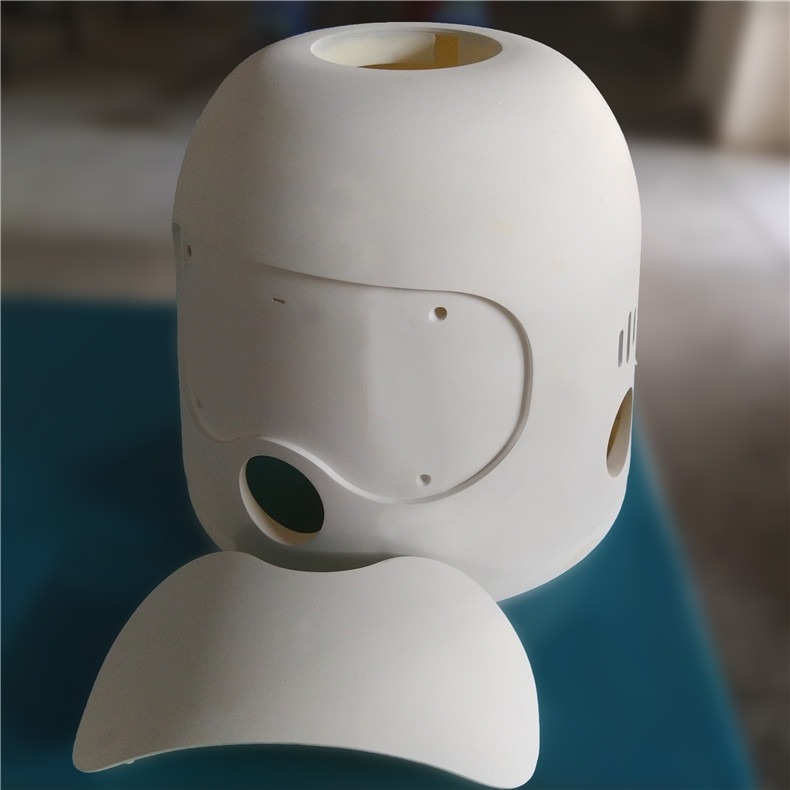
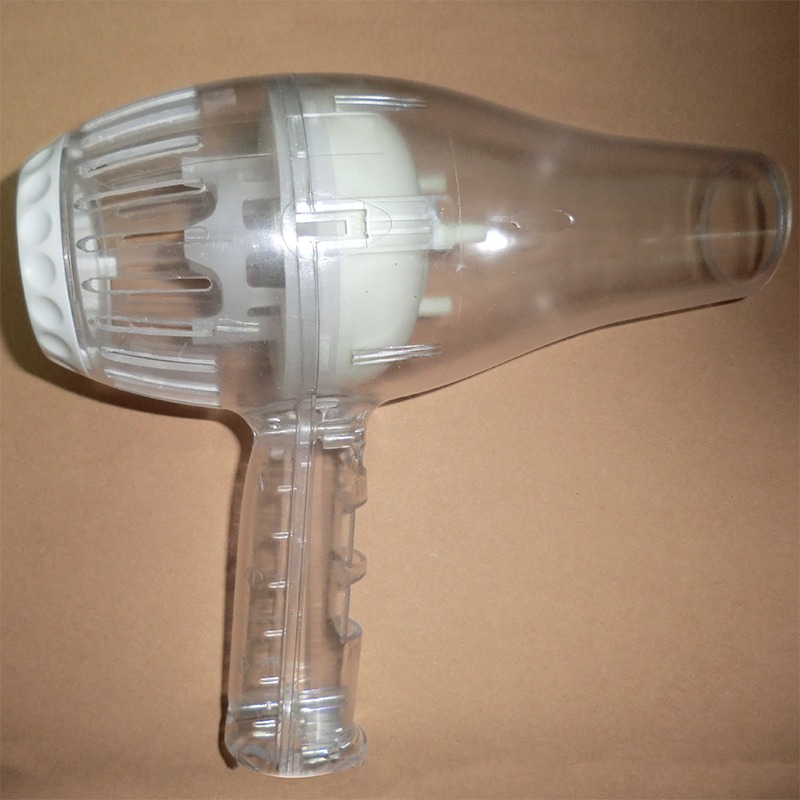
From Besten Blogs
How Besten prototype suggest to reduce the cost of cnc machined parts through structural design
CNC machining parts are parts processed by CNC equipment. CNC machining usually refers to a precision machining method controlled digitally by a computer. It has now become a common machining method.
CNC Plastic Machining for Acrylic CNC Machining
Acrylic CNC machining is a manufacturing process that uses computer-controlled machines to shape acrylic parts and components. It involves the use of CNC mills, lathes, routers, and other equipment to cut, drill, and shape acrylic materials into precise shapes and sizes.
CNC Plastic Machining: What Is It, Creating Prototypes, Operations, Materials
CNC plastic machining is a manufacturing process that uses computer-controlled machines to shape plastic parts and components. It involves the use of CNC mills, lathes, routers, and other equipment to cut, drill, and shape plastic materials into precise shapes and sizes.